Our Work with Tea Estates
Improving Fuel Efficiency and
Providing Workers with Electricity & Hot Water
Tea estates in Kenya are like independent states, having their own schools, health care, and social clubs, their own villages, factories and workshops. In the past, tea estates had upwards of 5000 employees, mostly tea pickers and wood cutters, but also factory workers, truck and tractor drivers, mechanics, and multi level managers. Many have since reduced their workforce to about 1500 people through mechanized harvesting. This enables them to improve the housing conditions for their remaining employees at a time of unprecedented demand for social equity.
Most farms have not yet electrified their housing clusters due to the clusters being in remote locations within walking distance of the fields. They are also not eager to increase fixed costs through grid extension, and solar is not practical due to mainly night-time use.
Housing on Kenyan tea estates is in very small rooms, typically three rooms per family, with four families in a single house. This arrangement, and the compact and geometric spacing of the houses, makes providing electricity quite easy and economical. Electric light is bright, spares cash spent on kerosene, and allows children of tea workers to study after dark. Cold water showers and laundry are done in communal bath houses, one bath house per 40 families, with separate sections for men and for women.
The VIP 10-40 Combined Heat and Power Plant supplies low-wattage lighting to 135 tea workers (35 Watts per worker), and hot water (35 to 45ºC) to 48 shower heads. The bath houses are connected with a loop of 1” diameter buried plastic pipe, both ends of which are connected to an elevated insulated hot water tank of 1200 liter capacity. At the tea estates the VIP 10-40 is run nine hours per day, from 4 am to 7 am and 4 pm to 10 pm, so as to ensure availability of hot showers and light while the workers are awake and at home.
Tea estates in Kenya cultivate eucalyptus trees to provide fuel for tea drying. The VIP 10-40 consumes 20 to 25 kilograms of wood per hour, or 250 kilograms per day, including bringing the boiler up to pressure. The wood is air-dried scrap wood from the tea factory sawmill.
Wood consumption by tea factories is typically 25 tons per day for 100 tons per day of green leaf. There is great interest in reducing wood consumption as many factories cannot process all of the tea that is available due to lack of fuel. We have tested several factory boilers with a combustion analyzer and found these to be not more than 60% efficient. As a result, Village Industrial Power has developed a simple boiler controller for optimizing furnace draft and air supply to increase efficiency, undergoing pilot testing in April 2022. Fuel savings of 10% (66% final efficiency) would make widespread use of the VIP 10-40 possible with no increase in total wood consumption.
Comment & Share
Other Posts
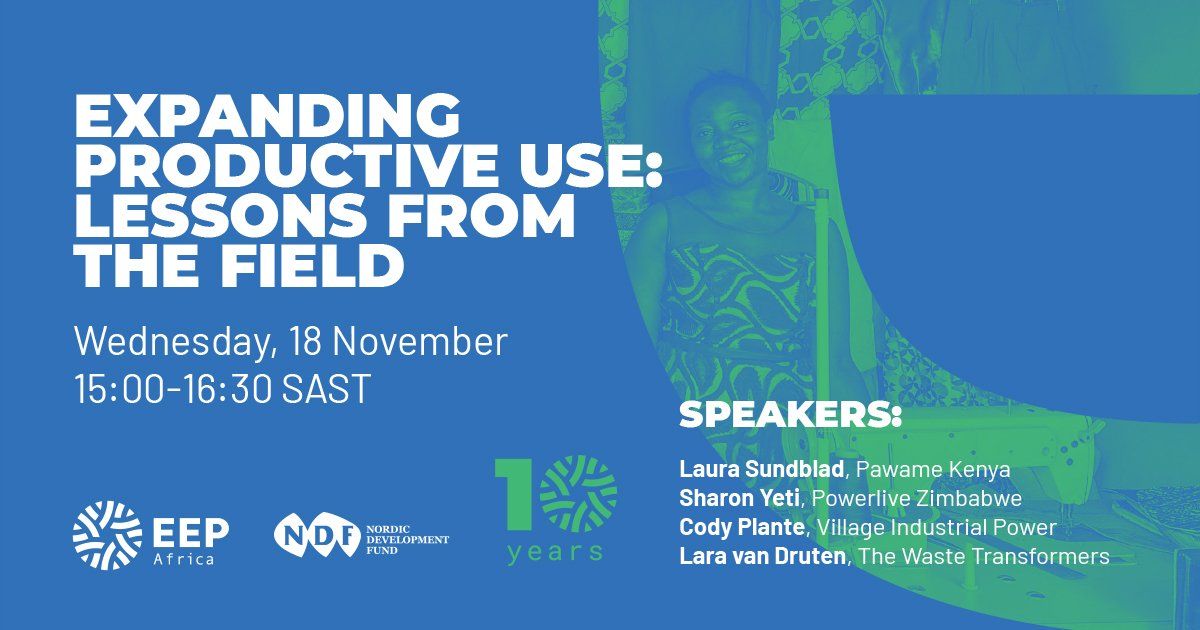
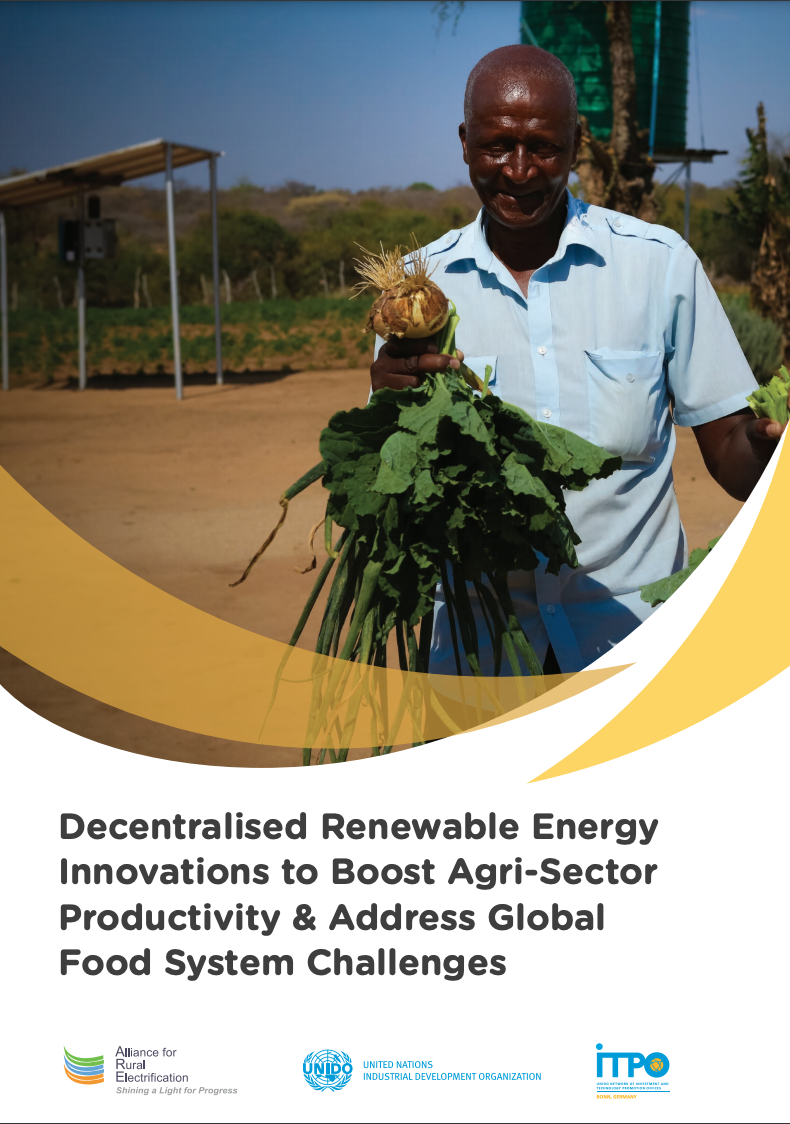
VIP Case Study Featured in Joint ARE UNIDO Publication on Decentralised Renewable Energy Innovations
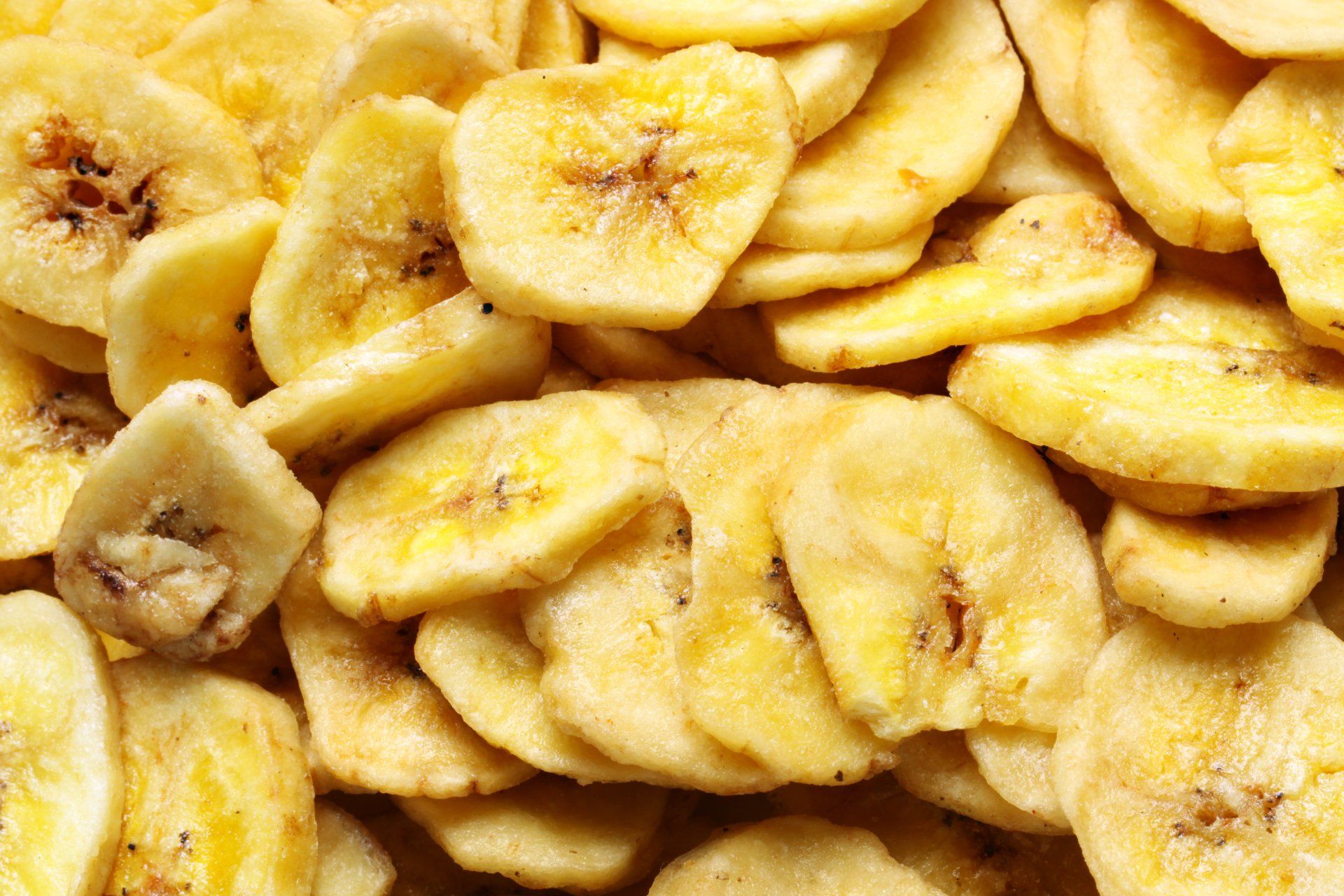
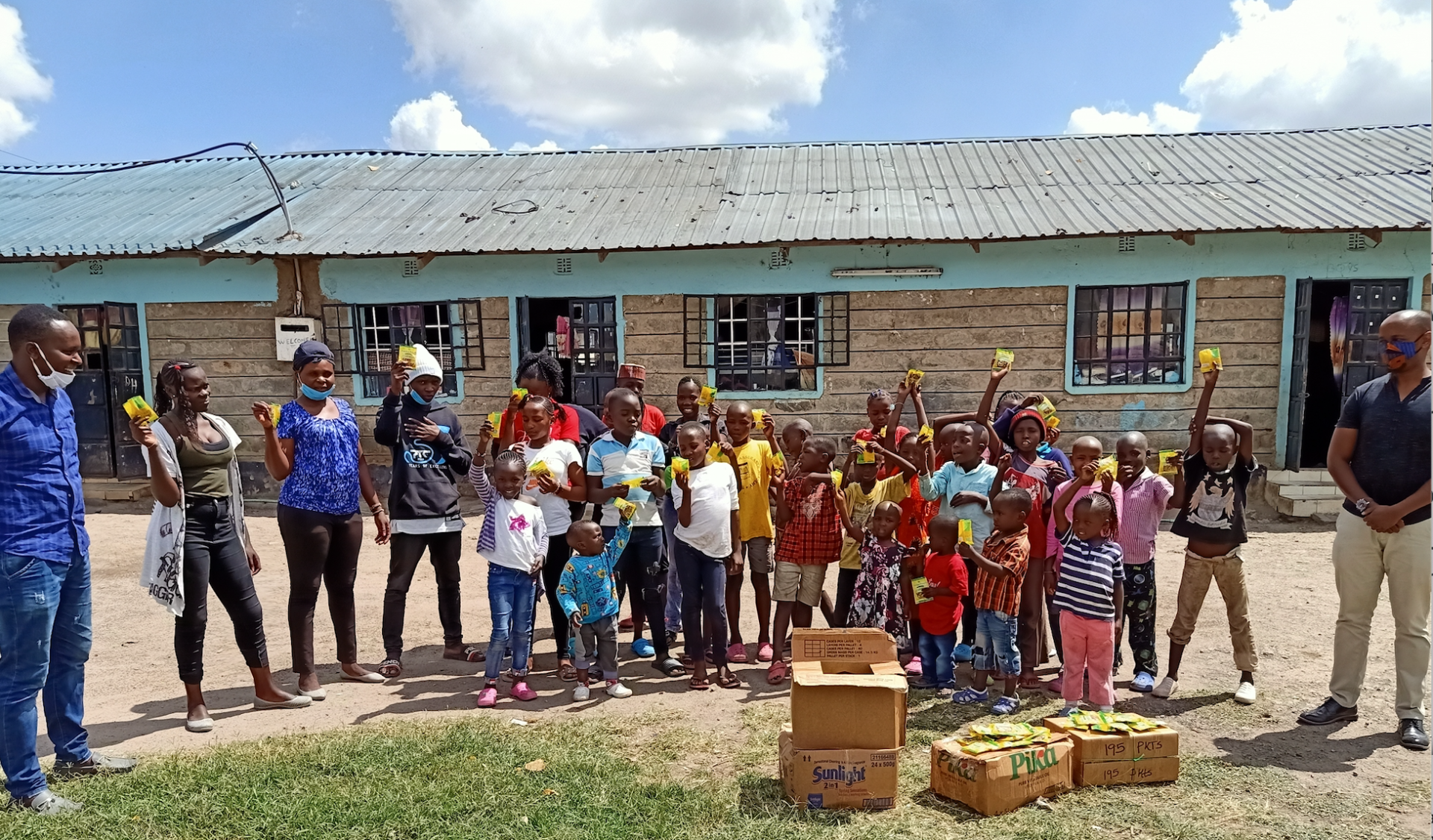
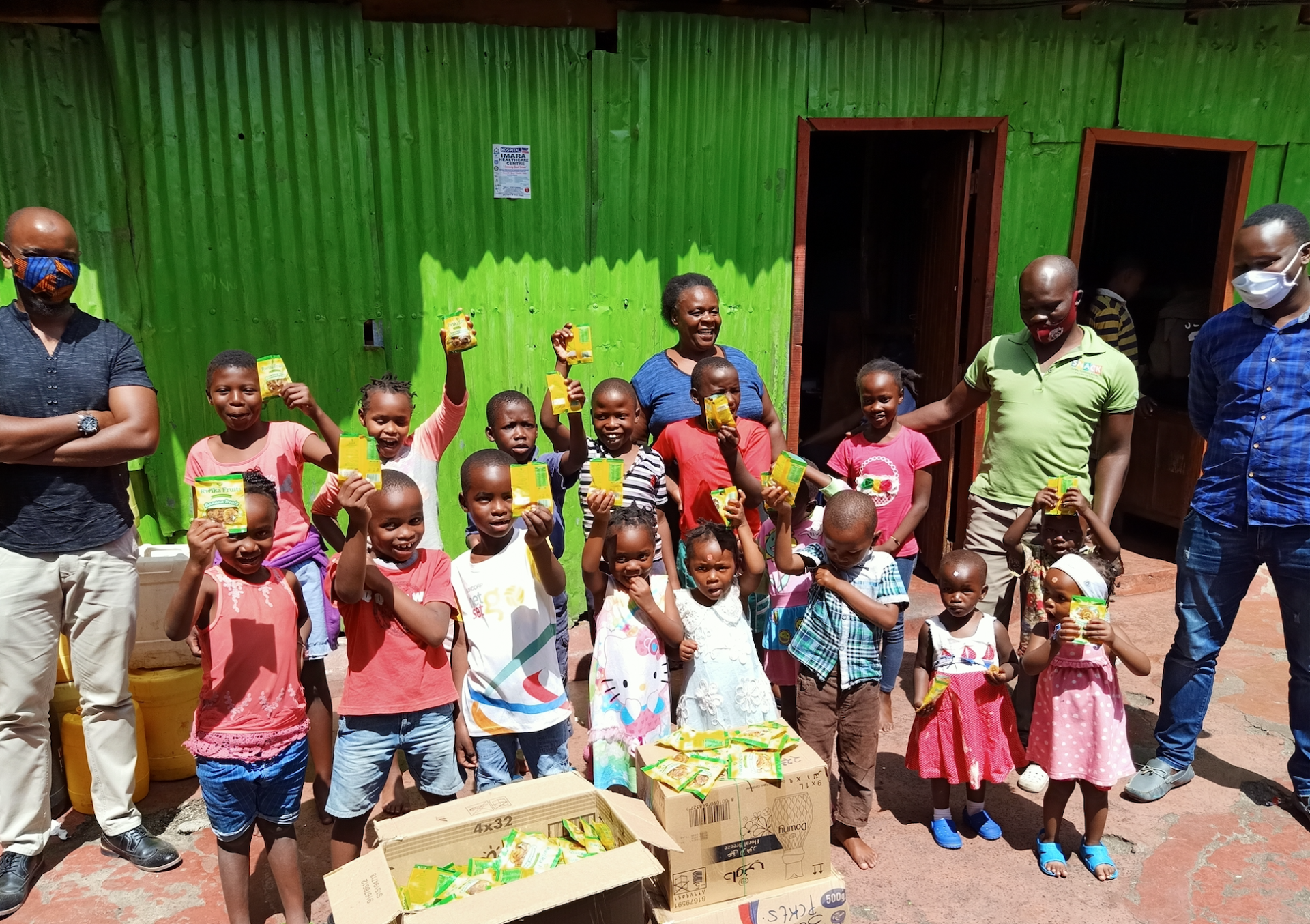